Customization
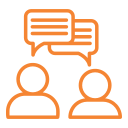
1. Demand communication:
Discuss product requirements in detail with customers, including design specifications, materials, dimensions, precision and other requirements, to provide a clear direction for subsequent work.
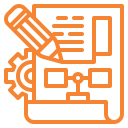
2. Design plan:
Professional design team preliminarily draws product design plans and generates drawing according to needs, and provides visual renderings and technical parameters for customer confirmation.
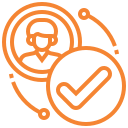
3.Customer confirmation:
Review the design plan and drawing with customers to ensure that all details meet the requirements, and enter the next stage after confirmation.
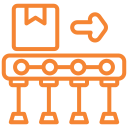
4.Product processing:
The actual processing and manufacturing of products are carried out in modern factories, and high-precision equipment is used to process products to ensure that the size and precision meet the design standards.
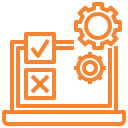
5. Product testing:
The processed products will be tested to test the product’s use effect, product size and function, and debug and optimize after problems are found.
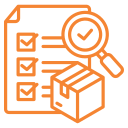
6. Final inspection and delivery:
After the product is qualified, the final quality inspection is carried out to ensure that the mold meets the customer’s requirements, and then production is carried out and delivered to the customer.
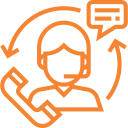
7. After-sales support:
Provide continuous technical support, including product maintenance, maintenance guidance and problem feedback processing to ensure the long-term use of the product.
This process ensures that our product customization is accurate and funny, providing customers with high-quality and compliant products.